Bei der Druckmessung stellen Sie möglicherweise fest, dass die Messergebnisse Änderungen des Eingangsdrucks nicht sofort widerspiegeln oder nicht vollständig übereinstimmen, wenn der Druck in seinen Ausgangszustand zurückkehrt. Wenn Sie beispielsweise eine Personenwaage zum Messen des Gewichts verwenden, benötigt der Sensor der Waage Zeit, um den Messwert Ihres Gewichts genau zu erfassen und zu stabilisieren. DerAnsprechzeitdes Sensors führt zu anfänglichen Datenschwankungen. Sobald sich der Sensor an die Last angepasst und die Datenverarbeitung abgeschlossen hat, zeigen die Messwerte stabilere Ergebnisse an.Hierbei handelt es sich nicht um einen Defekt des Sensors, sondern um eine normale Eigenschaft vieler elektronischer Messgeräte, insbesondere wenn es um Echtzeit-Datenverarbeitung und Steady-State-Erreichung geht. Dieses Phänomen kann als Sensorhysterese bezeichnet werden.
Was ist Hysterese bei Drucksensoren?
SensorHystereseTypischerweise tritt es auf, wenn sich der Eingang ändert (z. B. Temperatur oder Druck) und das Ausgangssignal nicht sofort der Eingangsänderung folgt, oder wenn der Eingang in seinen ursprünglichen Zustand zurückkehrt und das Ausgangssignal nicht vollständig in seinen ursprünglichen Zustand zurückkehrt . Dieses Phänomen ist an der Kennlinie des Sensors zu erkennen, wo es zwischen Ein- und Ausgang keine gerade Linie, sondern eine nacheilende schleifenförmige Kurve gibt. Insbesondere wenn Sie beginnen, den Eingang ab einem bestimmten Wert zu erhöhen, erhöht sich auch der Ausgang des Sensors entsprechend. Wenn die Eingabe jedoch beginnt, wieder auf den ursprünglichen Punkt abzusinken, werden Sie feststellen, dass die Ausgabewerte während des Reduktionsprozesses höher sind als die ursprünglichen Ausgabewerte und eine Schleife bilden oderHystereseschleife. Dies zeigt, dass während des Anstiegs- und Abfallvorgangs derselbe Eingangswert zwei unterschiedlichen Ausgangswerten entspricht, was der intuitiven Anzeige der Hysterese entspricht.
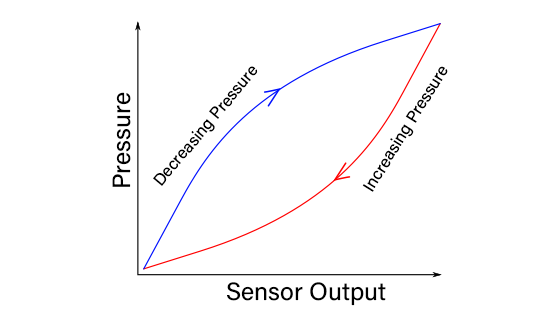
Das Diagramm zeigt den Zusammenhang zwischen Ausgangsleistung und anliegendem Druck in einem Drucksensor während des Druckbeaufschlagungsvorgangs, dargestellt in Form einer Hysteresekurve. Die horizontale Achse stellt die Sensorausgabe dar und die vertikale Achse den ausgeübten Druck. Die rote Kurve stellt den Prozess dar, bei dem die Sensorausgabe mit zunehmendem Druck zunimmt, und zeigt den Reaktionspfad vom niedrigen zum hohen Druck. Die blaue Kurve zeigt, dass mit abnehmendem angelegten Druck auch die Sensorausgabe abnimmt, vom hohen Druck zurück zum niedrigen, was die Reaktion des Sensors während der Druckentlastung darstellt. Der Bereich zwischen den beiden Kurven, die Hystereseschleife, zeigt den Unterschied im Sensorausgang bei gleichem Druckniveau während des Ladens und Entladens an, der typischerweise durch die physikalischen Eigenschaften und die innere Struktur des Sensormaterials verursacht wird.
Gründe für die Druckhysterese
Das Hysterese-Phänomen inDrucksensorenwird hauptsächlich von zwei Hauptfaktoren beeinflusst, die eng mit den physikalischen Eigenschaften und dem Funktionsmechanismus des Sensors zusammenhängen:
- Die elastische Hysterese des Materials Jedes Material erfährt eine gewisse elastische Verformung, wenn es äußeren Kräften ausgesetzt wird, eine direkte Reaktion des Materials auf die ausgeübten Kräfte. Wenn die äußere Kraft entfernt wird, versucht das Material, in seinen ursprünglichen Zustand zurückzukehren. Aufgrund der Ungleichmäßigkeit innerhalb der inneren Struktur des Materials und der geringfügigen irreversiblen Veränderungen der inneren Mikrostruktur bei wiederholter Be- und Entladung ist diese Wiederherstellung jedoch nicht vollständig. Dies führt zu einer Verzögerung des mechanischen Verhaltens bei kontinuierlichen Be- und Entladevorgängen, bekannt alselastische Hysterese. Besonders deutlich wird dieses Phänomen bei der Anwendung vonDrucksensoren, da Sensoren häufig Druckänderungen genau messen und darauf reagieren müssen.
- Reibung Bei den mechanischen Komponenten eines Drucksensors, insbesondere bei beweglichen Teilen, ist Reibung unvermeidlich. Diese Reibung kann von Kontakten innerhalb des Sensors herrühren, wie z. B. Gleitkontaktpunkten, Lagern usw. Wenn der Sensor Druck ausübt, können diese Reibungspunkte die freie Bewegung der internen mechanischen Strukturen des Sensors behindern, was zu einer Verzögerung zwischen der Reaktion des Sensors und der Reaktion führt tatsächlicher Druck. Wenn der Druck entlastet wird, können dieselben Reibungskräfte auch dazu führen, dass die inneren Strukturen nicht sofort stoppen und somit auch während der Entlastungsphase eine Hysterese auftreten.
Diese beiden Faktoren zusammen führen zu der Hystereseschleife, die in Sensoren bei wiederholten Belastungs- und Entlastungstests beobachtet wird, eine Eigenschaft, die bei Anwendungen, bei denen Präzision und Wiederholbarkeit sehr gefragt sind, oft von besonderer Bedeutung ist. Um die Auswirkungen dieses Hysteresephänomens zu reduzieren, ist eine sorgfältige Konstruktion und Materialauswahl des Sensors von entscheidender Bedeutung. In Anwendungen können auch Softwarealgorithmen erforderlich sein, um diese Hysterese zu kompensieren.
Das Hysterese-Phänomen inDrucksensorenwird von verschiedenen Faktoren beeinflusst, die direkt mit den physikalischen und chemischen Eigenschaften des Sensors und seiner Betriebsumgebung zusammenhängen.
Welche Faktoren führen zu einer Sensorhysterese?
1. Materialeigenschaften
- Elastizitätsmodul: Der Elastizitätsmodul des Materials bestimmt den Grad der elastischen Verformung bei Krafteinwirkung. Materialien mit einem höheren Elastizitätsmodul verformen sich weniger und ihreelastische Hysteresekönnte relativ niedriger sein.
- Poissonzahl: Die Poissonzahl beschreibt das Verhältnis von Querkontraktion zu Längsdehnung in einem Material unter Krafteinwirkung, das sich auch auf das Verhalten des Materials beim Be- und Entladen auswirkt.
- Interne Struktur: Die Mikrostruktur des Materials, einschließlich Kristallstruktur, Defekte und Einschlüsse, beeinflusst sein mechanisches Verhalten und seine Hystereseeigenschaften.
2. Herstellungsprozess
- Bearbeitungspräzision: Die Präzision der Bearbeitung von Sensorkomponenten wirkt sich direkt auf deren Leistung aus. Komponenten mit höherer Präzision passen besser und reduzieren zusätzliche Reibung und Spannungskonzentration, die durch schlechte Passform verursacht werden.
- Oberflächenrauheit: Die Qualität der Oberflächenbehandlung, wie z. B. die Oberflächenrauheit, beeinflusst das Ausmaß der Reibung und beeinflusst dadurch die Reaktionsgeschwindigkeit und Hysterese des Sensors.
- Temperaturänderungen beeinflussen die physikalischen Eigenschaften von Materialien, wie zum Beispiel den Elastizitätsmodul und den Reibungskoeffizienten. Hohe Temperaturen machen Materialien im Allgemeinen weicher, verringern den Elastizitätsmodul und erhöhen die Reibung, wodurch die Hysterese zunimmt. Umgekehrt können niedrige Temperaturen Materialien härter und spröder machen und die Hysterese auf unterschiedliche Weise beeinflussen.
3. Temperatur
- Temperaturänderungen beeinflussen die physikalischen Eigenschaften von Materialien, wie zum Beispiel den Elastizitätsmodul und den Reibungskoeffizienten. Hohe Temperaturen machen Materialien im Allgemeinen weicher, verringern den Elastizitätsmodul und erhöhen die Reibung, wodurch die Hysterese zunimmt. Umgekehrt können niedrige Temperaturen Materialien härter und spröder machen und die Hysterese auf unterschiedliche Weise beeinflussen.

Risiken
Das Vorhandensein einer Hysterese inDrucksensorenkann zu Messfehlern führen und die Genauigkeit und Zuverlässigkeit des Sensors beeinträchtigen. Bei Anwendungen, die hochpräzise Messungen erfordern, wie etwa bei der präzisen industriellen Prozesssteuerung und der Überwachung kritischer medizinischer Geräte, kann die Hysterese zu erheblichen Messfehlern führen und sogar zum Ausfall des gesamten Messsystems führen. Daher ist das Verständnis und die Minimierung der Auswirkungen der Hysterese ein wesentlicher Bestandteil der Gewährleistung eines effizienten und genauen Betriebs vonDrucksensoren.
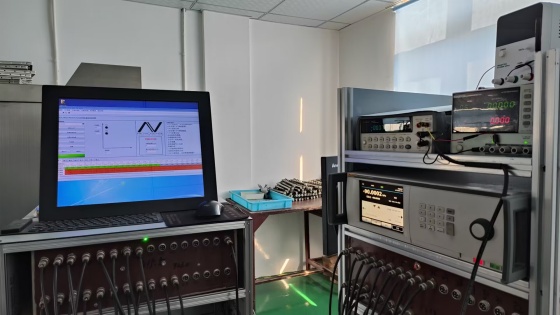
Lösungen für Hysterese in Drucksensoren:
Um möglichst geringe Hystereseeffekte zu gewährleistenDrucksensorenHersteller haben mehrere wichtige Maßnahmen ergriffen, um die Sensorleistung zu optimieren:
- Materialauswahl: Die Materialauswahl spielt eine entscheidende Rolle bei der Hysterese. Daher wählen Hersteller die im Sensorbau verwendeten Kernmaterialien wie Membranen, Dichtungen und Füllflüssigkeiten sorgfältig aus, um sicherzustellen, dass sie unter verschiedenen Arbeitsbedingungen eine minimale Hysterese aufweisen.
- Designoptimierung: Durch die Verbesserung des strukturellen Designs von Sensoren, wie z. B. Form, Größe und Dicke der Membranen, und die Optimierung von Dichtungsmethoden können Hersteller die durch Reibung, Haftreibung und Materialverformung verursachte Hysterese wirksam reduzieren.
- Alterungsbehandlung: Neu hergestellte Sensoren können eine erhebliche anfängliche Hysterese aufweisen. DurchAlterungsbehandlungund spezifische Testprogramme können Materialien beschleunigt werden, um sich zu stabilisieren und anzupassen, wodurch diese anfängliche Hysterese verringert wird. Das Bild unten zeigt dieXDB305durchmachenAlterungsbehandlung.
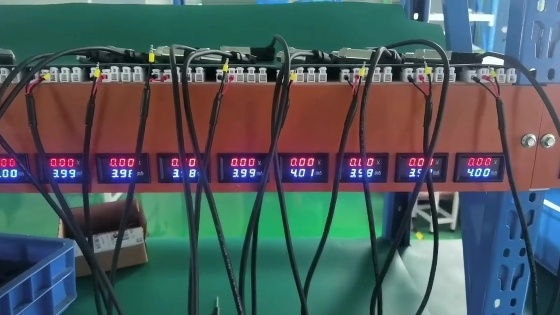
- Strenge Produktionskontrolle: Durch die strenge Kontrolle von Toleranzen und Qualität während des Produktionsprozesses stellen Hersteller die Konsistenz jedes Sensors sicher und minimieren die Auswirkungen von Produktionsschwankungen auf die Hysterese.
- Erweiterte Kalibrierung und Kompensation: Einige Hersteller nutzen fortschrittliche digitale Kompensationstechnologie und Mehrpunkt-Kalibrierungsmethoden, um die Hysterese in den Sensorausgängen präzise zu modellieren und zu korrigieren.
- Leistungstests und -bewertung: Alle Sensoren werden detaillierten Tests unterzogen, um ihre Hystereseeigenschaften zu bewerten. Basierend auf den Testergebnissen werden die Sensoren bewertet, um sicherzustellen, dass nur Produkte auf den Markt kommen, die bestimmte Hysteresestandards erfüllen.
- Beschleunigte Lebensdauertests: Um die Leistungsstabilität von Sensoren während ihrer erwarteten Lebensdauer zu überprüfen, führen Hersteller beschleunigte Alterungs- und Lebensdauertests an Proben durch, um sicherzustellen, dass die Hysterese innerhalb akzeptabler Grenzen bleibt.
Diese umfassenden Maßnahmen helfen Herstellern, das Hysterese-Phänomen effektiv zu kontrollieren und zu reduzierenDrucksensorenDadurch wird sichergestellt, dass die Sensoren in tatsächlichen Anwendungen hohe Genauigkeits- und Zuverlässigkeitsanforderungen erfüllen.
Zeitpunkt der Veröffentlichung: 09.05.2024